From Pushback to Progress: How Lean Six Sigma Practitioners Handle Change Resistance
- Peter Assad
- Oct 14, 2024
- 3 min read
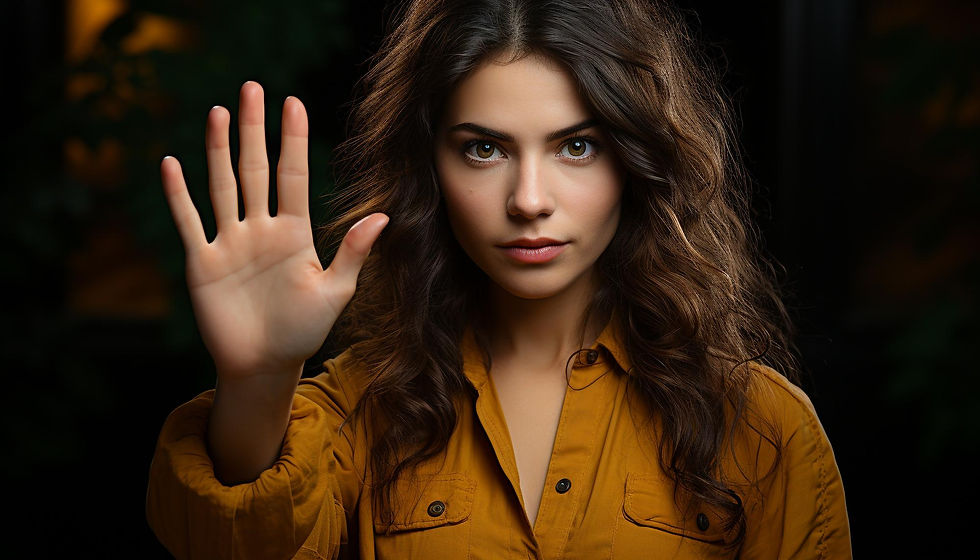
Implementing Lean Six Sigma in an organization involves more than just technical process adjustments; it necessitates significant cultural changes. Resistance to such changes is a common challenge that can derail improvement initiatives if not effectively managed. This blog post explores proven strategies that Lean Six Sigma practitioners can use to overcome resistance to change, integrating established Change Management methodologies to ensure successful and sustainable outcomes.

1. Engage Stakeholders Early and Often
One of the core principles of Lean Six Sigma is to involve the people who do the work in the improvement process. This same approach should be applied to Change Management. Engage key stakeholders, including employees, managers, and leadership, from the very beginning. Understand their concerns, get their buy-in, and empower them to contribute ideas and feedback.
Fact: Studies show that projects with high levels of stakeholder engagement are 6 times more likely to succeed than those with low engagement levels.
Strategy Implementation
Regular Feedback Sessions: Conduct regular meetings and feedback sessions with all stakeholders to discuss progress and gather input.
Inclusive Planning: Involve stakeholders in planning and decision-making processes to foster a sense of ownership and commitment.

2. Leverage Change Management Frameworks
Lean Six Sigma can be seamlessly integrated with established Change Management methodologies, such as Kotter's 8-Step Process, ADKAR, and Bridges' Transition Model. These frameworks provide a structured approach to navigating the people side of change, including building a sense of urgency, communicating the vision, and reinforcing new behaviors.
Strategy Implementation
Kotter’s Model: Use Kotter's steps to establish a sense of urgency, create a guiding coalition, and consolidate gains to produce more change.
Source: Click here
ADKAR Model: Focus on Awareness, Desire, Knowledge, Ability, and Reinforcement to support individual transitions.
Source: Click here
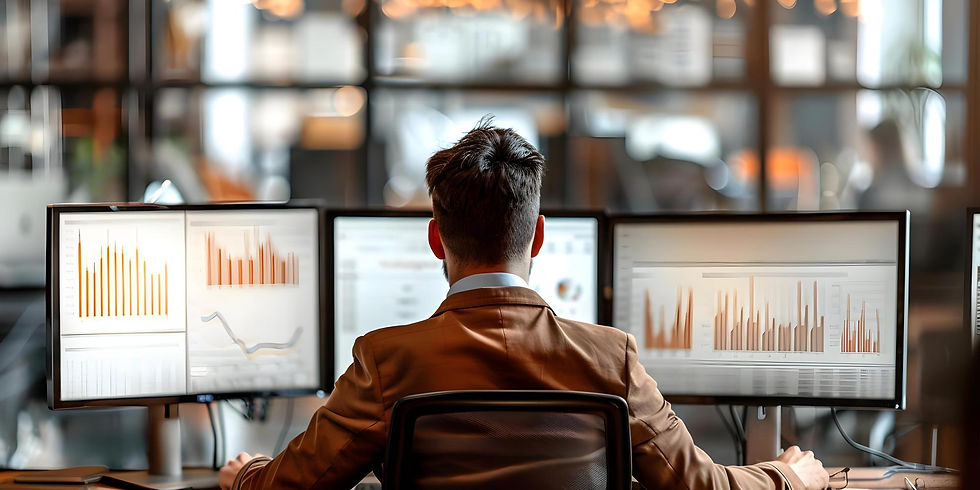
3. Use Data to Drive Decisions
A key principle of Lean Six Sigma is to use data and facts to drive decision-making. Apply this same approach to Change Management. Measure and analyze the current state, the desired future state, and the progress and impact of the change initiative. Use this data to build a compelling case for change and address any resistance or concerns.
Fact: Organizations that base their change initiatives on data-driven insights are 23% more likely to achieve sustainable performance improvements.
Strategy Implementation
Baseline Measurements and Continuous Monitoring: Establish clear metrics to measure the current state and track progress over time.
Transparent Communication: Share data and progress reports regularly to demonstrate the benefits and necessity of the changes.
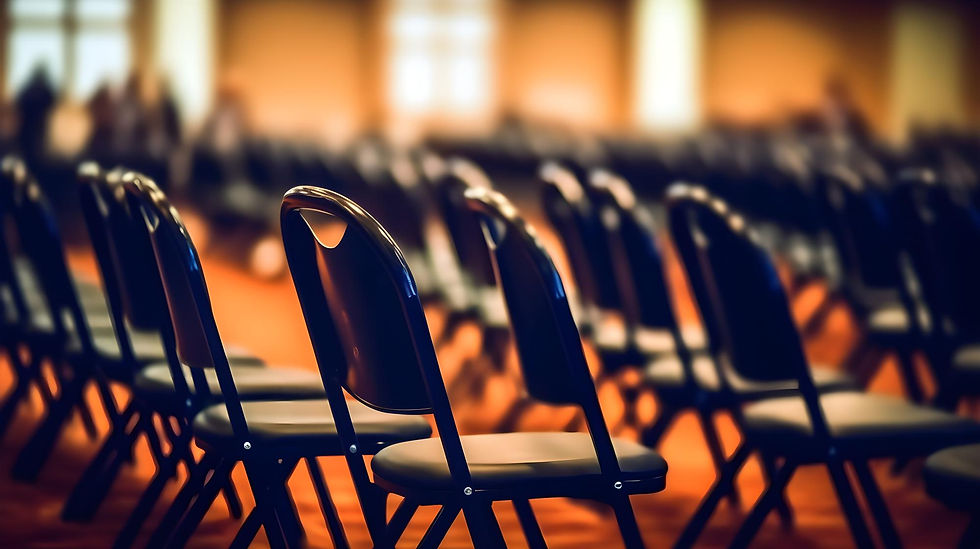
4. Provide Training and Support
Ensure that key stakeholders and employees understand the principles of both Lean Six Sigma and Change Management. Provide comprehensive training and workshops to familiarize them with the methodologies, their benefits, and how to apply them. Additionally, offer ongoing support and coaching to help people navigate the change process.
Fact: Effective training can increase project success rates by up to 50%, according to industry surveys.
Strategy Implementation
Customized Training Programs: Tailor training sessions based on the roles and responsibilities of participants.
Mentorship and Support Structures: Establish a system of mentorship where experienced practitioners help guide employees through the change process.

5. Celebrate Successes and Embed Changes
Using the "Control" stage of the DMAIC framework, ensure that improvements are sustained. Celebrate successes to reinforce new behaviors and integrate changes into the organization’s standard practices and policies.
The final phase of Lean Six Sigma's DMAIC framework is the "Control" stage, which focuses on sustaining the improvements over time. Apply similar principles to Change Management by celebrating successes, reinforcing new behaviors, and embedding the changes into the organization's standard practices and policies.
Fact: Recognizing and celebrating achievements can improve employee engagement by up to 60%.
Strategy Implementation
Recognition Programs: Develop recognition programs that publicly acknowledge the contributions of teams and individuals.
Policy Updates: Regularly update policies and standard operating procedures to reflect new practices.
Key Takeaways
Early and frequent engagement of stakeholders is essential for gaining buy-in and reducing resistance.
Change Management frameworks provide a structured approach to addressing the human aspects of Lean Six Sigma initiatives.
Data-driven decision-making is crucial for objectively managing change and demonstrating the benefits of new practices.
Comprehensive training and continuous support are pivotal in helping employees adapt to new ways of working.
Celebrating successes and institutionalizing new behaviors are critical for sustaining improvements.
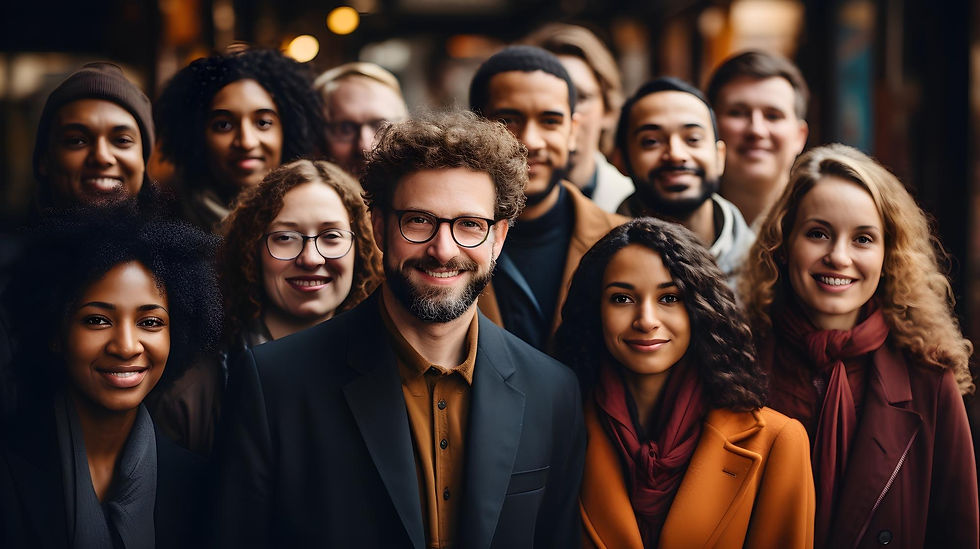
By adopting these strategies, Lean Six Sigma practitioners can effectively manage resistance to change, ensuring that process improvements are not only implemented but also embraced and sustained over time, leading to lasting benefits for the organization.