
In the realm of quality management and process improvement, Six Sigma stands as a distinguished methodology aimed at enhancing business performance by systematically removing waste, reducing variability, and improving the quality of products and services.
What Is Six Sigma?
Six Sigma is a data-driven approach and set of tools for process improvement, designed to help companies improve their operations, increase customer satisfaction, and boost their bottom line by minimizing errors and variability in business processes. It focuses on making processes more predictable and efficient, ultimately leading to a better quality of products and services. At its heart, Six Sigma is about achieving measurable and quantifiable financial returns for the organization.
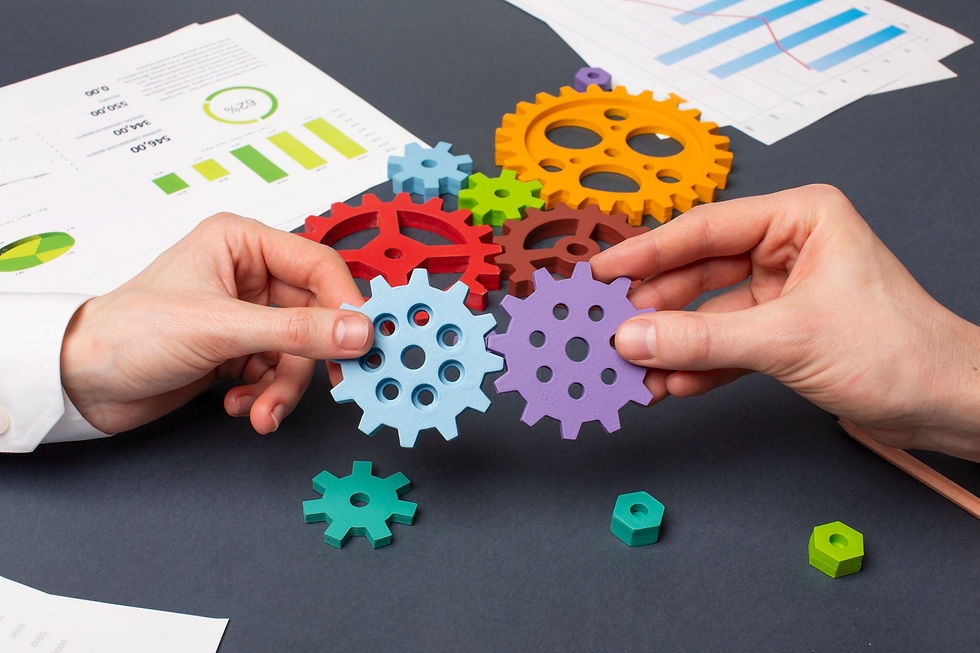
A Brief History of Six Sigma
The concept of Six Sigma was originally developed by Motorola in the 1980s as a way to improve manufacturing processes through the meticulous analysis of process data. Bill Smith, a Motorola engineer, is credited with inventing Six Sigma to address quality issues and improve production processes. The methodology was further popularized and refined by companies like General Electric, where under the leadership of Jack Welch in the 1990s, it became central to corporate strategy and business culture.

Benefits of Six Sigma
Implementing Six Sigma within an organization can lead to numerous benefits, including:
Reduced Costs and Increased Profits: By eliminating defects and waste, companies can significantly lower their operating costs and enhance profitability.
Improved Quality: Six Sigma methodologies help in achieving near-perfect quality, reducing the rate of defects to as low as 3.4 per million opportunities.
Customer Satisfaction: High-quality products and services lead to higher customer satisfaction and loyalty.
Enhanced Decision Making: Six Sigma's emphasis on data and statistical analysis aids in making more informed and effective business decisions.
Employee Engagement: Six Sigma projects often involve cross-functional team collaboration, which can increase employee engagement and foster a sense of ownership and accountability.
The Value of Six Sigma to Businesses
Six Sigma offers a structured and scientifically proven methodology for solving quality problems and enhancing operational efficiency. It is highly valued across various sectors for its ability to align a company’s processes with its strategic goals, thus ensuring that every facet of the operation contributes to overall success. By adopting Six Sigma, businesses can achieve a competitive edge, streamline operations, and ensure that quality improvement efforts are effectively yielding the highest possible return on investment.

Main Components of Six Sigma
The Six Sigma methodology is anchored around five key phases, known collectively as DMAIC, which stands for:
Define: Identify the problem or project goals within a process.
Measure: Quantify the current process performance.
Analyze: Determine the root causes of defects or variations.
Improve: Implement and verify solutions to address root causes.
Control: Maintain the improvements and ensure consistent performance over time.
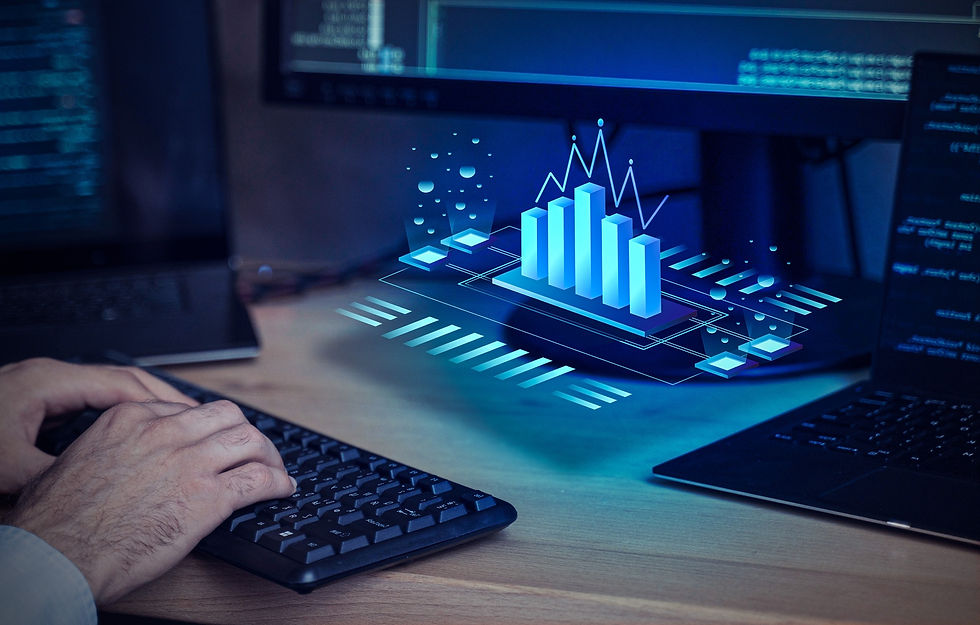
Key Facts and Figures
3.4 Defects Per Million Opportunities (DPMO): Six Sigma strives for a high standard of quality, aiming for no more than 3.4 defects per million opportunities.
Success Stories: Many Fortune 500 companies have reported substantial savings and revenue growth attributed to their Six Sigma initiatives. General Electric, for example, reported benefits of over $12 billion during the first five years of its Six Sigma implementation.

Key Takeaways
Six Sigma is a disciplined, data-driven approach focused on reducing variability in processes and eliminating defects to improve quality and efficiency.
Developed by Motorola and popularized by General Electric, Six Sigma has a rich history of contributing to quality improvement and operational excellence.
The methodology offers significant benefits, including cost reduction, quality improvement, enhanced customer satisfaction, better decision-making, and increased employee engagement.
Six Sigma's value to businesses lies in its ability to systematically improve processes, align operations with business strategy, and deliver measurable financial returns.
DMAIC (Define, Measure, Analyze, Improve, Control) provides a structured framework for implementing Six Sigma projects.

Six Sigma has emerged as a pivotal strategy for businesses aiming for excellence in quality management. Its proven track record in various industries underscores its effectiveness in tackling complex problems, enhancing operational efficiency, and achieving remarkable improvements in product and service quality. By integrating Six Sigma principles into their core practices, organizations can look forward to achieving higher levels of customer satisfaction, operational excellence, and sustainable business growth.