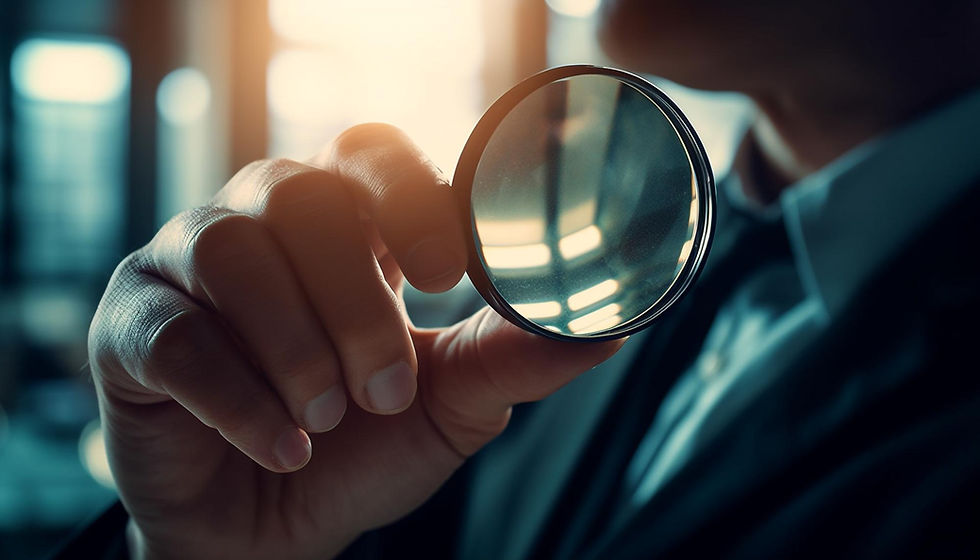
The traditional approach to maintaining quality in manufacturing and service industries has often leaned heavily on increased inspection. However, this method can be inherently reactive, focusing on identifying defects after they occur rather than preventing them at the source.
Lean methodologies offer a contrasting approach, emphasizing quality improvement through root cause analysis and process optimization. This shift not only enhances product and service quality but also reduces waste and increases efficiency.
Shifting from Inspection to Quality Improvement
The Limitations of Inspection
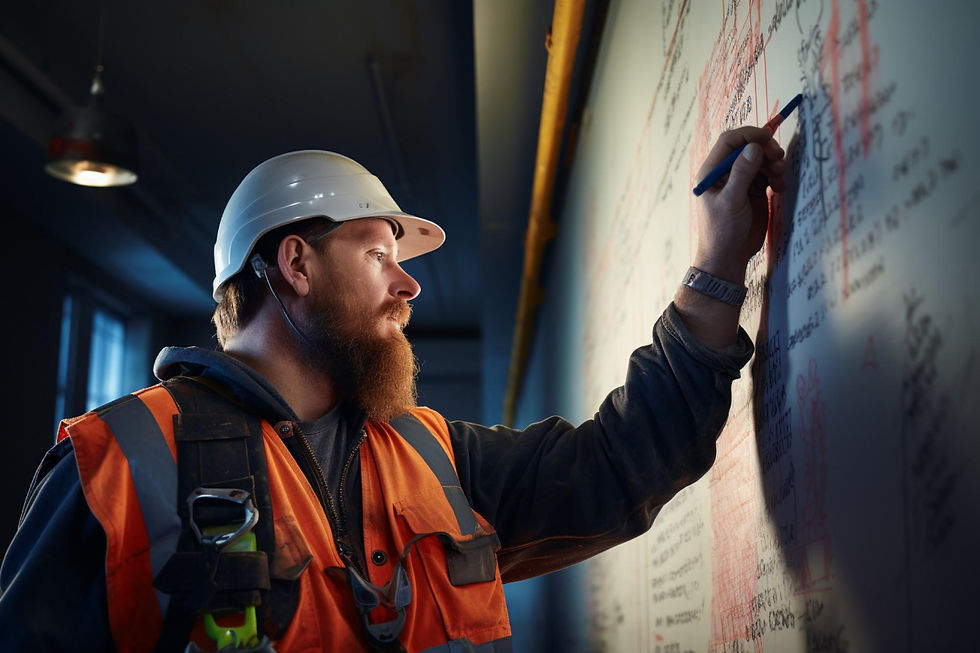
Inspection, particularly when used as the primary means of quality control, can lead to increased costs, delays, and a higher likelihood of defects slipping through, given its reactive nature.
Fact: Studies have shown that the cost of finding and fixing a defect post-production can be up to 30 times more than if it were identified and corrected at the design stage.
The Lean Approach to Quality

Lean methodologies advocate for building quality into the process from the start, focusing on root cause analysis to prevent defects before they occur. This proactive stance not only improves quality but also significantly reduces the need for inspection and rework.
Fact: Implementing lean quality improvement processes has led to defect reductions of up to 50% in manufacturing industries.
Key Strategies in Lean Quality Improvement
Root Cause Analysis
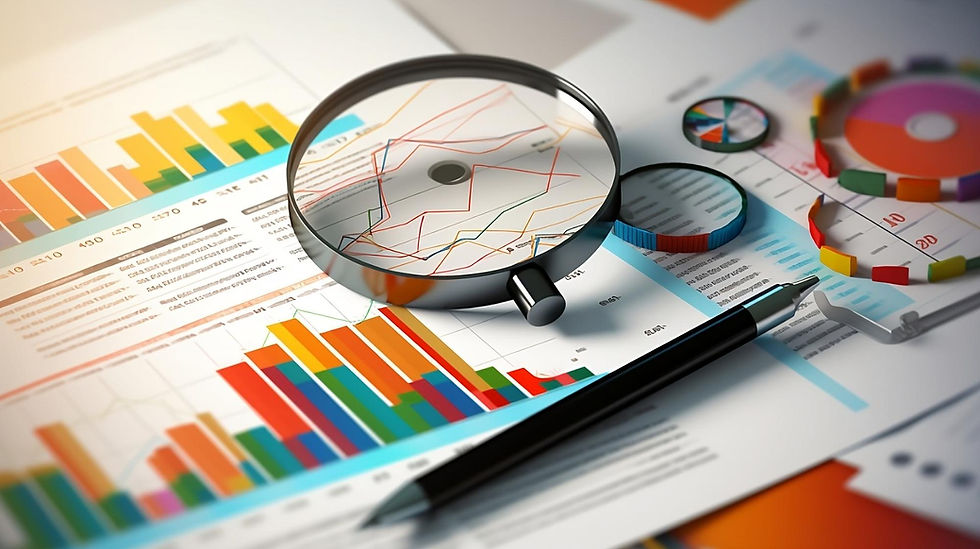
Using tools such as the Five Whys and Fishbone diagrams, Lean encourages teams to drill down to the underlying causes of defects, allowing for the implementation of systemic changes that prevent recurrence.
Fact: Companies that regularly perform root cause analysis report a 60% decrease in project failure rates.
Continuous Improvement (Kaizen)

Continuous improvement, or Kaizen, is a cornerstone of Lean, fostering an environment where employees at all levels are encouraged to suggest and implement improvements. This culture not only improves quality but also increases employee engagement and innovation.
Fact: Organizations that engage in continuous improvement practices see an average productivity increase of 25%.
Process Standardization
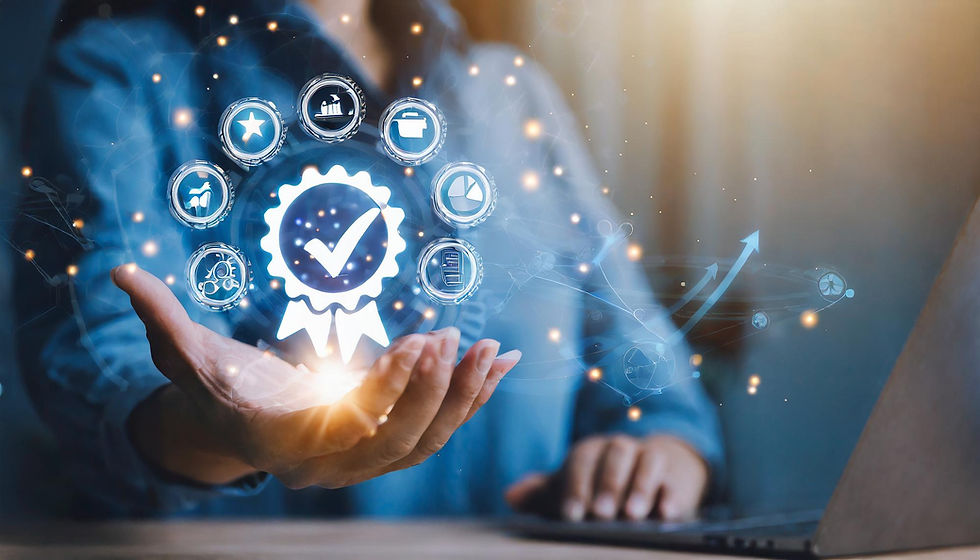
Lean emphasizes the importance of standardizing processes to ensure consistency in quality. Standardization helps to minimize variability, one of the main culprits behind defects.
Fact: After adopting process standardization, businesses have reported a 30% improvement in operational efficiency.
Quality Improvement vs. Inspection in Lean
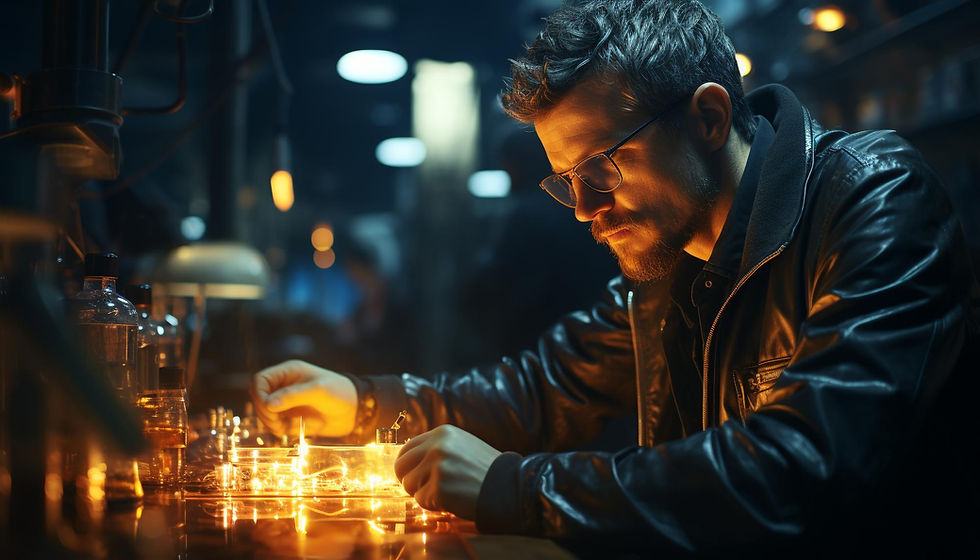
The Lean approach to quality improvement is fundamentally different from traditional inspection methods. By focusing on the root causes of defects and embedding quality into the process, Lean methodologies can achieve more sustainable and cost-effective results.
Financial Impacts and Key Facts
Reduced Costs: The shift from inspection to quality improvement can significantly reduce costs associated with rework, waste, and returns. Companies practicing Lean methodologies report saving an average of 15% of their total operational costs.
Increased Customer Satisfaction: High-quality products and services lead to higher customer satisfaction and loyalty, which can translate into increased revenue. Businesses focusing on quality improvement see an average increase in customer satisfaction scores of 20%.
Operational Efficiency: Lean's focus on quality improvement leads to smoother operations, as processes are optimized and defects are minimized. This results in shorter cycle times and increased throughput.
Key Takeaways
The traditional emphasis on increased inspection can be costly and ineffective, often addressing symptoms rather than underlying causes of defects.
Lean methodologies offer a proactive approach to quality improvement, focusing on root cause analysis and process optimization to prevent defects before they occur.
Adopting a Lean approach to quality can lead to significant financial savings, improved operational efficiency, and higher customer satisfaction.
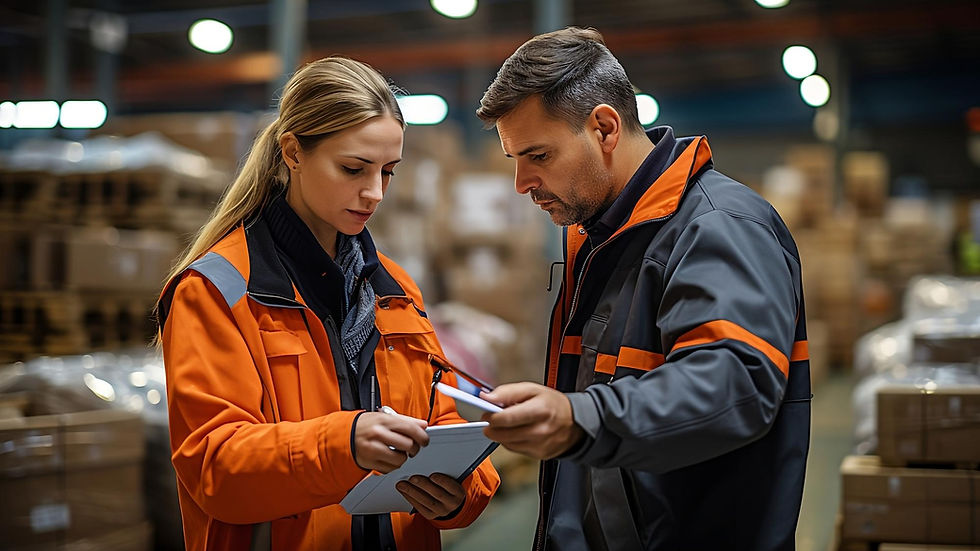
Embracing the Lean approach to quality over increased inspection not only enhances product and service quality but also aligns with the principles of efficiency and waste reduction at the heart of Lean methodologies. This shift from a reactive to a proactive stance on quality control can lead to more sustainable business practices and long-term success.