Single Piece Flow vs. Batch Processing: Making the Right Choice
- Peter Assad
- Mar 21, 2024
- 3 min read

In the realm of manufacturing and operations management, the debate between single piece flow and batch processing methodologies is a longstanding one. Both approaches have their unique benefits and drawbacks, and choosing the right one depends on various operational contexts and objectives.
Single Piece Flow

Single piece flow refers to the process of moving one work item through all steps of the manufacturing process without waiting, from start to finish, before moving on to the next piece. This method is closely aligned with Lean manufacturing principles.
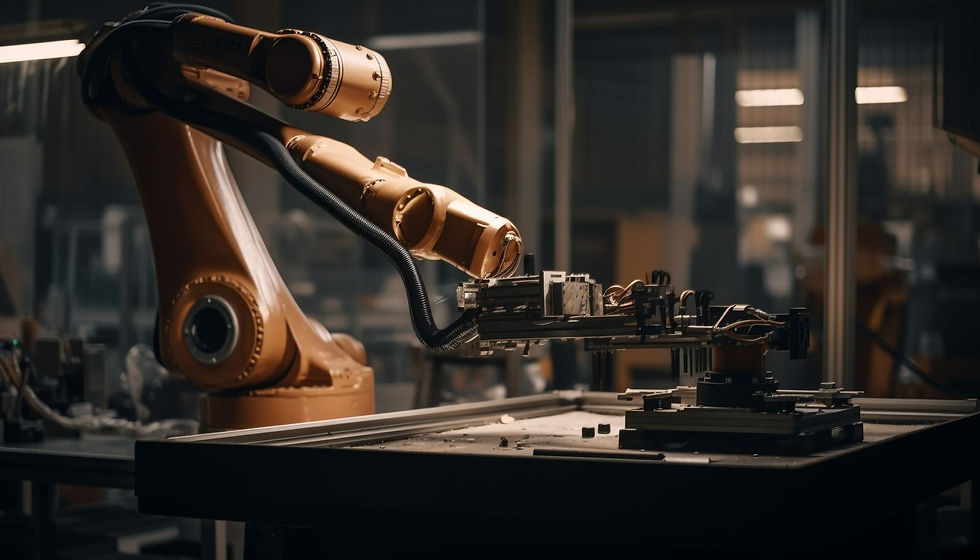
Benefits
Reduced Lead Times: By eliminating the wait times between operations, single piece flow can significantly decrease overall lead times.
Lower Defect Rates: It enables immediate identification and correction of defects, reducing the overall defect rate.
Increased Flexibility: Adjustments can be made quickly, allowing for greater flexibility in responding to customer demands and changes.
Improved Employee Engagement: Workers are involved in a variety of tasks, which can increase job satisfaction and decrease turnover.

Drawbacks
Higher Setup Times: Frequent changes between tasks might increase setup times, affecting efficiency.
Limited Scalability: In cases of high-volume production, single piece flow may not be as efficient as batch processing.
Fact: Implementing single piece flow has been shown to reduce lead times by up to 90% in some industries.
Batch Processing

Batch processing involves completing a batch of work items at one operation before moving the entire batch to the next operation. This method is often used in traditional manufacturing settings.

Benefits
Economies of Scale: Producing in batches can reduce the cost per unit by spreading the setup costs over a larger number of items.
Higher Throughput: For operations with long setup times, batch processing can result in higher overall throughput.
Simplified Planning: Planning and scheduling can be simpler when dealing with batches rather than individual items.

Drawbacks
Increased Inventory Levels: Batches waiting for the next operation can lead to increased inventory levels and associated costs.
Hidden Defects: Defects may not be discovered until late in the process, potentially affecting large numbers of items.
Less Flexibility: Responding to changes in customer demand or correcting defects can be more challenging with batch processing.
Fact: Batch processing can lead to inventory carrying costs that are 20-30% of the total production cost.
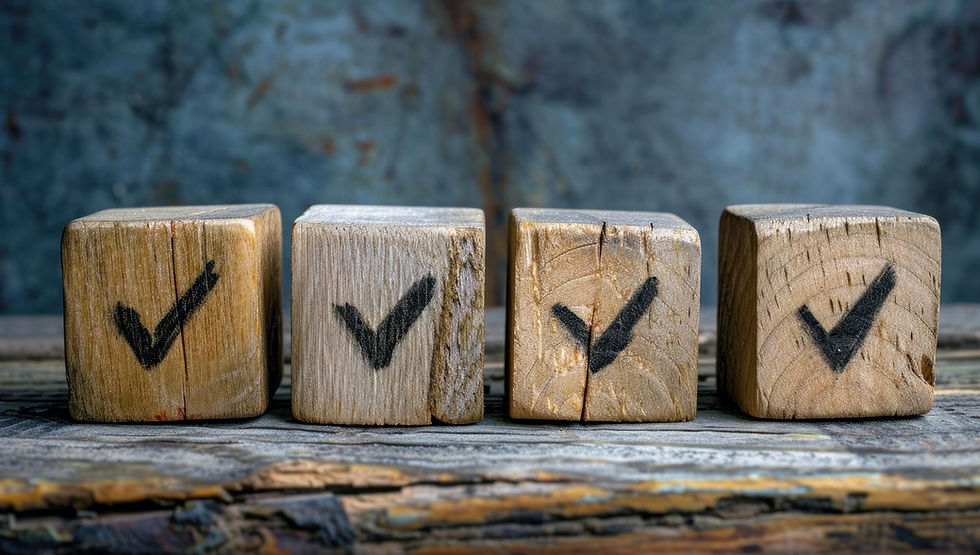
Making the Right Choice
The choice between single piece flow and batch processing depends on several factors, including the nature of the product, production volume, variability in customer demand, and the specific goals of the operation.
High-variability, Low-volume Operations: Single piece flow is often more suitable for customized products or operations where flexibility and responsiveness are critical.
High-volume, Low-variability Operations: Batch processing may be more efficient for products with stable demand patterns and where economies of scale can be realized.
Key Takeaways
Single piece flow offers reduced lead times, lower defect rates, increased flexibility, and improved employee engagement but may face challenges with higher setup times and limited scalability.
Batch processing can achieve economies of scale and higher throughput but may lead to increased inventory levels, hidden defects, and less flexibility.
The choice between single piece flow and batch processing should be informed by an analysis of production volume, demand variability, product nature, and operational goals.

Understanding the strengths and limitations of each approach allows businesses to optimize their operations, ensuring efficiency, quality, and responsiveness to customer needs. Adapting the strategy to fit the specific context of the operation is key to achieving operational excellence.